Operational Excellence: Do Companies Need to Implement it?
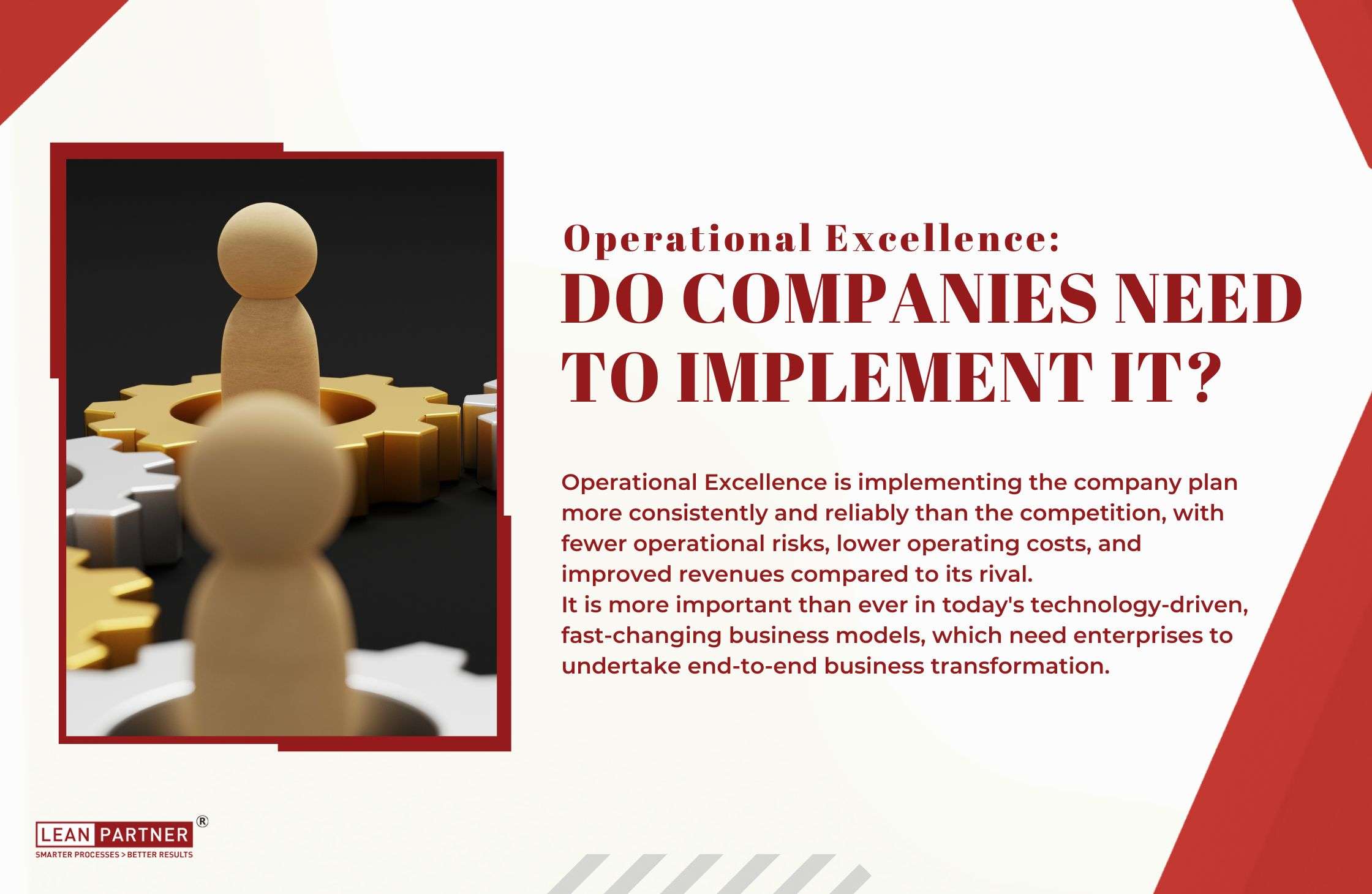
When an organization stops expanding, it ceases to improve. However, identifying particular areas for development might be challenging. The procedure may be complex and often necessitates significant adjustments. However, in certain circumstances, change happens more subtly – slowly and gradually over time. One example is operational excellence.
This article will discuss operational excellence and how a firm may attain it. Let’s get started and learn more about operational excellence.
Table Of Contents
What is Operational Excellence?
Operational Excellence is implementing the company plan more consistently and reliably than the competition, with fewer operational risks, lower operating costs, and improved revenues compared to its rival. It is more important than ever in today’s technology-driven, fast-changing business models, which need enterprises to undertake end-to-end business transformation. Operational excellence may also be defined as execution excellence.
Lean Manufacturing, lean six sigma, Kaizen, Hoshin Planning, Balanced Scorecard, and other essential process approaches are used.
However, the goal of Operational Excellence extends beyond standard continuous improvement approaches to a long-term shift in corporate culture. Companies pursuing Operational Excellence do two things considerably differently than other companies: they manage their business and operational processes methodically and engage in establishing the proper culture.
Operational Excellence is shown by integrated performance across revenue, cost, and risk. It focuses on exceeding customer expectations by continuously improving operational procedures and organizational culture. The objective is to create a single, integrated enterprise-level management system with perfect flow. The second element, a culture of operational discipline, is typically defined as doing the right thing, the right way, every time. This culture is based on the guiding values of honesty, questioning attitude, constant problem-solving, daily continuous development mindset, degree of knowledge, collaboration, and process drive.
Why Do Businesses Need To Adopt Operational Excellence?
The road to business operational excellency requires commitment, patience, and, most importantly, a grasp of Continuous Improvement. Effective business and process improvement may help your firm in the following major areas if you apply the corresponding methods and methodologies efficiently:
- Alignment of your strategy and culture.
- Work and goals must be in sync.
- Enhancement of decision-making performance.
Three Operational Excellence Methodologies
Lean Manufacturing
Lean Manufacturing is concerned with removing waste from the manufacturing process while maintaining productivity. In other words, it tries to develop business procedures that accomplish high quality, safety, and worker morale while also lowering costs and cutting lead times.
Furthermore, waste is any action or spending of resources that do not provide value in the eyes of the client. There are seven categories of waste recognized in lean manufacturing:
- Overproduction in comparison to the plan
- Waiting time for workers and machinery
- Unnecessary transportation
- Process waste
- Material and component surplus
- Motion with no added value
- Quality flaws
Lean Six Sigma
lean six sigma is a compilation of tools and procedures for improving business operations. The purpose is to enhance the customer experience by identifying and eliminating variations. This may be performed by applying DMAIC, a lean six sigma sub-methodology. DMAIC is an acronym for:
- Define: define the issue in order to solve it.
- Measure: collect all available data and examine your operations in more depth.
- Analysis: examine your results to determine the source of the issue.
- Improvement: After you’ve studied your data, look for potential solutions and put them into action.
- Control: ensure that your newly installed procedure is maintained.
Kaizen
Kaizen is Japanese and means “Continuous Improvement.” It refers to initiatives aimed at implementing beneficial, continuing improvements at the workstation. In other words, it is a method that requires all workers at all levels of the organization to collaborate and act proactively in order to achieve frequent, incremental changes to the production process.
Kaizen emphasizes the value of a continuous improvement. It is not enough to make adjustments once; organizations must make a consistent effort to improve. Numerous businesses have used Kaizen’s philosophy and technique to boost staff productivity, save expenses, and enhance the entire customer experience.
What Are the Operational Goals?
Methodologies like lean six sigma, Lean Management, Kaizen, and the Shingo Model are used to achieve operational excellence. Each approach has its own set of guiding principles to assist you in making choices.
However, when adopting any new process or program in your firm, defining specific objectives is a great practice. Setting goals makes it simpler to calculate your ROI.
Let’s take a look at the many sorts of operational objectives to consider while developing your strategy.
1. Operational-Oriented Goals
Operational objectives aim to increase firm productivity and improve product or service quality. Two examples of goals are increasing safety precautions and improving product or service adaptability.
2. Financial-Oriented Goals
Finance objectives seek to enhance financial indicators. These ongoing improvements are the consequence of improved operations, stronger customer connections, and higher customer value. They are often the outcome of increasing earnings, lowering expenditures, and producing free cash flow.
3. People-Oriented Goals
Finally, people-oriented objectives focus on workforce and cultural activities that are vital to an organization’s operational excellency. Some examples are growing employee participation in operational excellence activities, boosting skill training, and enhancing staff productivity.
What Industries Stand to Gain from Operational Excellence?
Because operational excellence ideas focus on process, a well-planned program may assist a wide range of sectors. Distinct sectors, however, will seek to optimize different processes.
The following are some of the industries that benefit from operational excellence:
Manufacturing
Manufacturing companies are no strangers to operational improvement efforts. As the Fourth Industrial Revolution takes root, industries are under pressure to boost efficiency, reduce downtime, and eliminate waste wherever possible.
Construction
Construction, like Chevron, places a premium on employee health and safety as a metric of operational excellence performance.
Holcim Switzerland and Italy, for example, used the Beekeeper employee communication app to improve operational health and safety messaging across their scattered workforce.
Healthcare
Like many others, the healthcare business continually seeks ways to minimize costs while still providing excellent patient care.
According to McKinsey, acute-care hospitals are focused on lean operations, clinical uniformity, and supplier utilization to achieve clinical operations excellence and unlock savings.
Continuous Improvement vs. Operational Excellence
To comprehend operational excellence, it is necessary first to grasp the notion of continuous improvement. While they are alike, they are not the same.
Continuous improvement refers to an organization’s ongoing attempts to enhance its processes, services, or products. The procedure usually happens gradually over time and does not need any substantial adjustments or ground-breaking innovation. It is critical for a firm to improve and continue to create and retain improvements; however, constant progress cannot be sufficient on its own.
As the firm refines its goods, services, or procedures, it must endeavor to maintain its growth. This is where the notion of operational excellency comes into play.
To accomplish long-term progress, operational excellence incorporates specific techniques and ideas. When all people of a business can clearly understand the flow of value to the customer, the mentality has been reached.
Seeing the value stream, however, may not be enough; firms must actively focus on enhancing both the value offer and its delivery. However, operational excellence involves more than just boosting production or lowering expenses. It is about strengthening traditional work culture and delivering highly useful services and goods for your consumers in order to achieve long-term, sustainable development.
The term “journey” might be used to characterize operational excellence. The path entails locating the appropriate instruments for the relevant tasks. When they all work together, the firm achieves the ideal organizational culture in which people feel inspired and empowered.
Conclusion
Because it incorporates several processes, the transfer of value, and many other factors, operational excellence is a multifaceted topic. Operational excellence is more crucial than ever, and your company needs it NOW.
Companies that do not develop or strive for operational excellence generally struggle to build a name for themselves.
Whether you operate a small firm or a huge corporation, managers may transform processes by using lean six sigma and other similar concepts to achieve operational excellence. Furthermore, if the complexity of the operational excellence procedure is too much to handle, you can rely on operational excellence consulting firms or take operational excellence courses.