Combating organizational problems and criticisms with lean six sigma
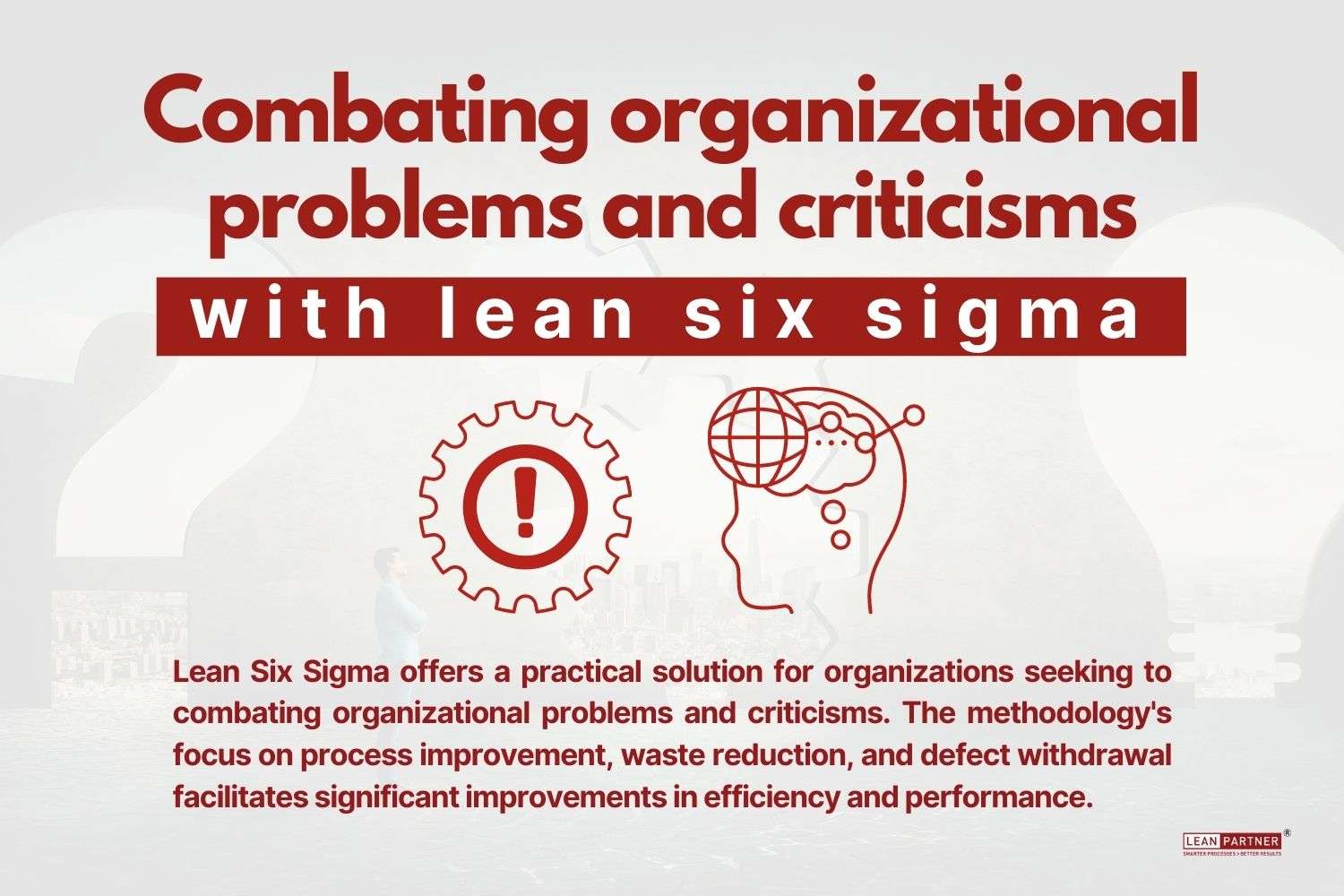
Are you finding it challenging to combating organizational problems and criticisms hampering your company’s growth and success? If yes, then you’re not the only one.
Organizational problems and criticisms can significantly impact a company’s work, reputation, and bottom line. From poor communication to inefficient processes, these issues can arise from different factors and be challenging to resolve.
However, there is a solution that can help conflict these issues and streamline your organization’s processes – lean six sigma. By applying this methodology, companies can improve their efficiency, reduce waste, and ultimately enhance their overall performance.
This article will explore how lean six sigma can help combat organizational problems and criticisms. We will provide an in-depth understanding of the concept, its benefits, and its methodology. We will also showcase a real-life case study to demonstrate the effectiveness of lean six sigma in resolving organizational issues. So, if you want to improve your organization’s performance and combat its problems and criticisms, keep reading.
Table Of Contents
Understanding Organizational Problems
Organizations often face many challenges that can hamper their growth and success, such as inefficient processes, poor communication, lack of quality control, and other issues that can result in decreased productivity and revenue. These problems can also lead to criticisms of the organization, damaging its reputation and spoiling stakeholder confidence.
Companies can use the lean six sigma methodology to combat these organizational problems and criticisms. This approach is based on data-driven decision-making and aims to reduce defects and improve efficiency in processes. It achieves this by analyzing data, identifying inefficiencies, and implementing solutions to optimize processes.
By adopting the lean six sigma methodology, organizations can create a culture of continuous improvement, ensuring that they always strive to improve. The approach is particularly effective in addressing common organizational problems, such as bottlenecks in the supply chain or manufacturing processes, and it can help companies become more agile and responsive to changing market conditions.
Lastly, combating organizational problems and criticisms is essential for the success of any organization. By adopting the lean six sigma methodology, companies can address these issues head-on, improving their operations, boosting their reputation, and ultimately, increasing their bottom line.
How Lean Six Sigma Combats Organizational Problems and Criticisms
The Lean Six Sigma methodology is a practical approach to combating organizational problems and criticisms. It assumes a systematic and data-driven process of recognizing, analyzing, and solving issues.
A key strength of Lean Six Sigma is its focus on identifying and addressing the root causes of problems. Rather than merely treating symptoms, organizations can use various proven tools and techniques to tackle organizational problems and criticisms effectively.
In order to combat organizational problems and criticisms, Lean Six Sigma begins by categorizing issues according to their frequency and impact. This allows organizations to prioritize the most pressing issues and develop targeted solutions to address them.
Data and analytics also play an important role in the Lean Six Sigma approach. Through accurate analysis, organizations can gain insights into the underlying causes of problems. Provided with this knowledge, they can develop customized solutions that address the root causes of issues and prevent similar problems from arising in the future.
The design problem-solving process of Lean Six Sigma is another key aspect that ensures complete problem-solving. This organized approach ensures that issues are thoroughly understood and solutions are effective and sustainable.
In summary, the Lean Six Sigma methodology offers a powerful solution for combating organizational problems and criticisms. Its data-driven and systematic approach enables organizations to prioritize issues, address root causes, and develop targeted and continuous solutions. By using Lean Six Sigma, organizations can deliver high-quality services that meet the needs of stakeholders.
Examples of Successful Lean Six Sigma Implementations
The execution of Lean Six Sigma has proven to be highly successful across a broad range of industries. By embracing this methodology, organizations have improved operational efficiency, quality control, and customer satisfaction.
General Electric is a prime example of a company successfully joining Lean Six Sigma into its culture. Since the late 1990s, the company has applied Lean Six Sigma practices, leading to over $2 billion in cost savings.
Motorola is another organization that has demonstrated the effectiveness of Lean Six Sigma. As one of the early adopters of the methodology, Motorola achieved a remarkable 94% reduction in defects and a 70% reduction in cycle time.
In the healthcare sector, the Mayo Clinic has also experienced positive outcomes from implementing Lean Six Sigma. The clinic reported a 20% reduction in patient wait times and a 32% decrease in errors.
Other prominent organizations that have implemented Lean Six Sigma with notable success include Ford, Caterpillar, and Amazon.
These examples illustrate the effectiveness of Lean Six Sigma in enhancing organizational performance across various industries. By implementing Lean Six Sigma, organizations can realize cost savings, improve efficiency, and raise the overall quality of their products and services.
Challenges in Implementing Lean Six Sigma
Implementing Lean Six Sigma presents a set of challenges that organizations must overcome to adopt the methodology successfully. While the benefits of Lean Six Sigma are well-established, the following obstacles can hamper the effectiveness of Lean Six Sigma initiatives.
One of the primary challenges is employee resistance to change. Implementing new procedures and techniques may be met with resistance from employees who are accustomed to existing processes. Without buy-in and commitment from employees, the implementation may fail to deliver the intended benefits.
Training and development needs are other potential challenges. Implementing Lean Six Sigma requires employees to be trained in the methodology, tools, and techniques. Depending on the organization’s size, this can be costly and time-consuming.
A lack of leadership support is also a potential obstacle. If senior leadership is not fully committed to the implementation and does not provide adequate resources, support, and guidance, the implementation may falter.
Implementing Lean Six Sigma can present several challenges for organizations, but these can be overcome with the right approach. Employee resistance to change can be mitigated through effective communication, education, and engagement. Organizations can also ensure successful implementation by investing in training and development programs that build the skills and knowledge required for the methodology.
Leadership support is essential to the success of Lean Six Sigma initiatives, and organizations should work to establish a culture of commitment to the methodology throughout all levels of the organization. By providing adequate resources, guidance, and support, leaders can help ensure successful implementation.
Conclusion
In conclusion, Lean Six Sigma offers a practical solution for organizations seeking to combating organizational problems and criticisms. The methodology’s focus on process improvement, waste reduction, and defect withdrawal facilitates significant improvements in efficiency and performance. While implementing Lean Six Sigma can pose challenges, organizations can overcome them through effective communication with employees, investing in training and development, securing leadership support, and establishing accurate metrics for success. The long-term advantages of Lean Six Sigma make it a wise investment for organizations looking to achieve sustainable success in today’s competitive business landscape. By using Lean Six Sigma, organizations can improve their operation, increase customer satisfaction, and realize measurable benefits.