Training & Certification Malaysia
All the training and certification programs blend theoretical knowledge with practical application. Our customer experience training stands out as a key component, equipping every leader in Malaysia with the skills to deliver exceptional service and drive customer satisfaction.
Lean Six Sigma Programs
Driving process efficiency & effectiveness to achieve significant cost reduction & optimize process performance
Our certifications for Lean Six Sigma including Business Improvement Programs and Customer Experience Training Malaysia are designed to integrate seamlessly with Lean Six Sigma methodologies. At Lean Partner, we ensure our Lean Six Sigma courses in Malaysia are tailor-made to specifically meet the specific needs of each client, based on their industry.
These programs are made interesting and practical through the application of many simulations developed by us to enhance the learning experience of every participant. Participants attending Lean Six Sigma courses in Malaysia at Lean Partner undergo a rigorous process, ensuring they are well-prepared to apply Lean Six Sigma principles in real-world scenarios.
Lean Six Sigma courses in Malaysia at Lean Partner are aligned with internationally recognized certifications, which exemplify professionalism and high standards.
Lean Programs
Driving process efficiency & effectiveness to achieve significant cost reduction & optimized process performance
At its core, lean maximizes productivity while minimizing waste. In the world of lean, value is everything the customer is willing to pay for. At the end of the day, your focus should be on delivering value to the customer, and if they’re not willing to pay for a product, there is no value in that product. We work with our clients, primarily smaller and medium-sized service and operation organizations, hands-on and side-by-side to achieve their strategic and operational goals and objectives through the innovative application of Lean principles, methods, and tools.
Operational Excellence Programs
Accelerate your digital transformation with Operational Excellence
We work with organizations to realize measurable improvements that unlock value and create long-term sustainable growth. Our clients benefit from our expertise and experience to help organizations drive profitability and create growth through innovative application. Organisations that are leveraging new technologies and data insights to build more effective ways to operate are gaining a competitive advantage. Build better strategies based on real consumer sentiments and insights to inform your content and Customer Experience execution and develop hyper-targeted strategies based on your campaign goals and recommendations of key metrics.
Executive Leadership Programs
A sense of belonging and confidence by leading the organization in disruptive times
Building on cutting-edge research, Lean Partner’s executive leadership programmes will develop your ability to drive faster decision-making, accelerate change processes, and cut through difficult cultural challenges. It will provide you with a set of concepts and tools enabling you to lead your organisation with impact and efficiency – maximizing its performance in changing times. Our programmes are made relevant for executives preparing to transition into such roles in the near future.
Business Analytics Program
Achieve fluency in business strategies by making Data-Driven Business Decisions
Lean Partner’s Business Analytics programmes provide an introduction to big data analytics for all business professionals, including those with no prior analytics experience. It involves an iterative, methodical exploration of an organization’s data, with an emphasis on statistical analysis, to drive decision-making. You’ll learn how data analysts describe, predict, and inform business decisions in the specific areas of marketing, human resources, finance, and operations, and you’ll develop basic data literacy and an analytic mindset that will help you make strategic decisions based on data. You’ll apply your skills to interpret a real-world data set and make appropriate business strategy recommendations.
Project Coaching
Driving success: Tailored project coaching for Lean Six Sigma Project Leaders
Our Project Coaching Program is designed to empower Lean Six Sigma Green Belt and Black Belt project leaders with the guidance and support they need to execute DMAIC projects effectively within their organizations. This program provides a structured approach to overcoming common challenges in project execution, helping leaders gain control over their projects, build strong relationships with stakeholders, and showcase their value by delivering impactful, measurable results.
Through one-on-one coaching and practical, hands-on support, participants will develop critical skills to manage project complexities, drive continuous improvement, and ensure project outcomes align with organizational goals. Whether you’re seeking to refine your approach, enhance collaboration, or achieve targeted results, this program is tailored to equip you with the tools and confidence to lead successful projects that make a lasting impact.
Program Modulation
Our team of specialists collaborated to create this digital tool called Operational Excellence Navigator.
After conducting the survey, receive a personalized report with insights and recommendations to evaluate and enhance Operational Excellence (OPEX) in your organization.
It should take approximately 20 minutes to complete the assessment.
Consultative related articles
Leadership Development Guide: Master Change Management in 2025
Discover how business process improvement consultancy revolutionize efficiency and drive digital transformation. Optimize operations with expert guidance!
Digital Transformation Consultancy Driven Empowerment: Transforming Businesses and Lives
Discover how business process improvement consultancy revolutionize efficiency and drive digital transformation. Optimize operations with expert guidance!
Testimonials

“The Trainer sharing sessions were very enjoyable, easy to understand as the examples he used are simple and related to real life.”

“The explanation from the trainer that help us to understand that this course can help us in our work experience”

“All the samples (diagrams like project charter and fishbone method) that can be implemented straight away”

“Manica have a very skillful training method and informative. Useful reading material and text book.”

“Notes and content of the message is precise and understandable.”

“Many side stories and tools that are insightful and applicable.”

“Trainer is very experienced and can explain each of the topics very clear.”

“Learned how to apply the DMAIC in daily work with many examples shared by trainer.”
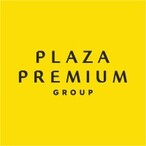
“Identify opportunities is important to improve a process for establishing a goal.”

“Eye opener for me to experience through lean six sigma method and I can identify waste process in my department.”

“This session help to clear my understanding about SS tool selection for my project”

“The practical experience from facilitator”

“There are a lot of activities and the trainer make it easy to understand”

“Understand about lean and six sigma. This is definitely improves my skill and knowledge”

“Sharing of projects that shows effectiveness of Lean Six Sigma”

“Clear and concise explanation of Lean Six Sigma”

“I feel more motivated and excited to implement in my daily work because I can clearly seen the direction of the work process now.”

“The practical examples on why and how the tools are being applied; the inspiring stories shared by Manica which help us to prepare for the real world challenges.”

“Great breakout activities session to engage with other participants. Good instructor with high presentation skill and examples.”

“Mr Robyn is a very good trainer - he breaks down complex theories in a easy to understand manner”

“Explanation by trainer is easy to understand using great training materials provided”

“The trainer is very engaging and accomodating the training session especially for non-bmr staffs.”

“Exploring how the tools are beneficial towards project execution. Great sharing by the trainer ”

“Robyn is very well versed with Lean and explained principles of Lean clearly. He is very patient in answering our questions and provided a very clear feedback to us”

‘’Completed my LSS Black Belt Certification with Lean Partner Sdn Bhd and I'm very happy with the training provided by well experienced trainers. A highly recommended place to pursue your LSS certification.’’

‘’The experience of the instructor, how lean sic sigma can be applied to our work and how to evaluate our current project whether is a go or no.. the knowledge .I love how the way it design. Cause it just flow perfectly’’

“Manica has been the 'wow' factor for me 🙂 he is very nicely smartly blended the manufacturing banking processes to hospital & ensure we get the point straight”.
