The 5 Lean Six Sigma Implementation Mistakes

Six Sigma is a methodology for process improvement that has been around for decades. Motorola coined the term, but it’s now used to refer to any number of similar methods. Lean Six Sigma is a set of tools and techniques that allows organizations to analyze, measure, and improve their processes to meet customer expectations, reduce waste and variability in their goods or services, and increase revenues through more efficient methods.
In this article, we discuss five common mistakes companies make when implementing Six Sigma projects – hopefully, this will help you avoid these pitfalls when starting your project!
Effective Leadership
Effective leadership means leaders must be able to communicate the importance of Lean Six Sigma to their teams. They should be able to share the vision and goals of Six Sigma. In addition, leaders should be able to explain what Lean Six Sigma problem definition is and what it is not—and why these two things are essential.
Also read: 10 Leadership Skills for Workplace Success
When first implementing Six Sigma tools, it’s also essential that leaders create an environment where employees feel comfortable asking questions or voicing concerns they may have about the implementation process. When employees feel like they can speak up without fear of retribution, you will see faster results!
Lean Six Sigma Strategy Making
Strategy making involves determining the best way to achieve your objectives, considering all available resources, constraints, and opportunities. Strategy making is a process that helps you to develop a plan for achieving your goals and objectives. It is also a tool that allows you to identify the best way to reach your goals.
Training and Certification
It’s essential to recognize training and certification as two separate things. Training is a must; certification, on the other hand, can be done by anyone. You can explore the different belt levels of Lean Six Sigma: Yellow Belt, Green Belt, and Black Belt in detail.
While you might think that anyone with a degree in business administration or engineering would be well-equipped to lead your team through Lean Six Sigma implementation challenges, it’s not necessarily true. The best candidate for training and certification should have experience in Six Sigma problems and solutions because they’ll be able to explain the concepts more clearly than someone without that background.
Project Selection
As the first step in implementing Six Sigma, select a project. The right project can make or break your program. You might think this is obvious, but many companies have failed to implement Six sigma implementation examples because they picked the wrong projects. If you want to succeed with Six Sigma principles, here are some things to keep in mind:
- Select projects that are important to the business. This seems like a no-brainer, but many companies choose their initial projects based on what’s easy instead of meaningful. They might select low-hanging fruit like reducing scrap rates or improving delivery time for customers who don’t complain about wait times or order accuracy—when those problems aren’t hurting sales and customer satisfaction! Instead of going after easy wins, pick high-impact initiatives that will make a massive difference for your bottom line.
These include cutting costs and increasing revenues by implementing new technologies (or updating old ones) and eliminating waste at every step in production processes. Hence, they’re faster and cheaper overall!
Responsibility
As a leader, you must ensure that all members of the organization understand their roles and responsibilities. You must be clear about what you expect from your team. When you fail to define clear roles for people, they will not put in as much effort because they do not know what is expected of them or how their work fits into the organization’s greater mission.
When there is no clarity about who is responsible for what, problems arise. Without clear ownership and accountability, people become confused about where they fit in and how their actions affect others in the company. This leads to poor communication across departments and teams, ultimately hurting productivity at every level of an organization’s structure.
Conclusion
By now, you know what the Lean Six Sigma problem definition is and how Lean Six Sigma is a powerful tool for improving your business, but it’s not something you can toss into the mix and expect results.
If you want to implement Six Sigma implementation steps in your organization, there are some things you need to know first. Interested in joining Lean Six Sigma training & certification at Lean Partner? Join us today.
Transform Your Business Efficiency with Leading Operations Management Consultants. Reach out to us now to see how we can help you excel.
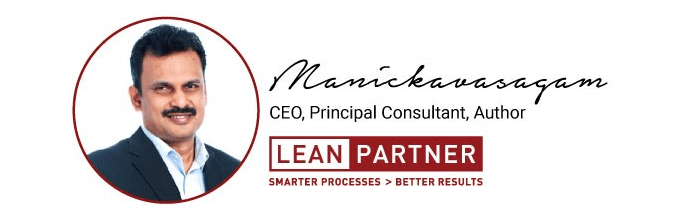