The Top 10 Lean Six Sigma Tips Worth Remembering
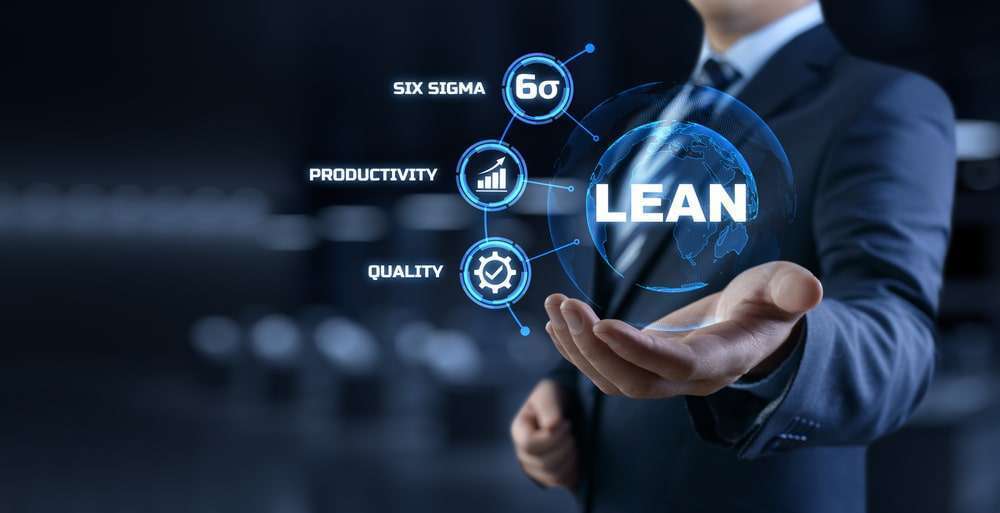
Today, while the world is already transitioning, lean six sigma is making its way much brighter as being one of the best process improvement methodologies used in almost every industry. In fact, with lean six sigma implementation, various enterprises increased their efficiency. Big names like Motorola, GE, Toyota, and many more are already celebrating their success by implementing lean business education. And many industries across the globe are also trying to do the same by implementing useful six sigma tips and methods.
But the main concern is how you will find out whether six sigma is suitable for your business or not? So, to sort out this confusion, first, you have to know the importance of implementing lean six sigma in your company. So, without proper understanding, lean six sigma won’t benefit your business as much as it can with proper understanding. For this, We bring the top 10 lean six sigma tips to successfully implement this methodology in your business.
Let’s have a look.
Top Ten Six Sigma Tips
The most common mistake people make while implementing Lean Six Sigma is the over-complexity of its directions. So, to timely deliver the projects and show increased efficiency, these are some lean Six Sigma tips that you and your business might need to follow.
We All are Customers too!
We must remember that we have customers, but we are also customers! If you want to succeed in any project or business, you must discuss what you need from your sponsors, colleagues, related departments, or suppliers. Always communicate in the best way regarding these things and try to explain the impact of such things on your project clearly. It is considered quite important practice in the implementation of Lean Six Sigma.
Be Open Eyed To Improving
There’s usually an opportunity to make minor improvements everywhere, even if you don’t work on strategy-changing projects. Regularly making minor improvements will result in a significantly more capable process over time so that you can develop a better understanding of Lean Six Sigma. In reality, the sum of the parts can be greater than the whole.
In light of technological advancement, best practices, and changing customer needs, there will always be a better way. Make sure you look for these opportunities constantly and encourage others to do so.
Everyone is Busy so Effort Requires a Reason
If you want somebody to go the extra mile, you should give them a good reason to do so. That means being obvious about what you want, when, why, and how it will directly impact stakeholders (including those you’re asking for support).
They won’t join you on the journey if they don’t understand the benefits of the destination you’re seeking.
Change Requires Minds and Hearts
Businesses are taking on more projects and ventures, which means even great ideas must be sold repeatedly. If you want to motivate people around you toward your project, you’ll need to understand what makes them do so and describe how your idea will help them.
Use Pareto’s Law, the 80/20 rule, where you and your stakeholders strategize so that 20% of your activities have maximum impact on shaping the project and don’t remain occupied with the novel, brainstormed ideas.
A complex Analysis Requires a Simple Conclusion
Your analysis is your journey, and your conclusion can be your destination. However, in business terms, stakeholders are always interested to know the destination, no matter how interesting your journey was. The simpler the conclusions, the quicker you can get to the way of approval. Lay out your conclusions first and then use your analysis to add support. Always keep them very simple and easily understandable, and make communication faster.
Getting Ahead with an Advocate
A little help goes a long way when the going gets challenging. Implementing organizational change will be easier if you have potent advocates. Ideally, your advocates should include executives, senior management, project champions and sponsors, and opinion formers at all levels.
If these potential advocates are not on your side, you need to find out why and see what can be done to align their views with yours. This will help you to accomplish your goals quicker and get the proper backing from the start. Work on this as early as possible to avoid future project stalls and minimize frustration.
Persistence Should be Admired, but Only Up to a Point
If it’s going to take a lot of struggle and time to prove your valid point, this has to be worth it– for you and your sponsor. Persistence is an admirable quality to achieve success, but you have to be sure of when to move with it or not. You must be very passionate and keen to be persistent in relevant but alternative projects to ensure long-term success.
Need of Strong Communication
The need to communicate may seem self-evident, but ensuring it’s a two-way process is essential. Sometimes little or no feedback indicates agreement, but it can also mean your message didn’t get through to the right level or has been ignored. Change is not readily accepted in organizations, it is often viewed as just too difficult or dismissed without consideration.
So be it if you need to adapt or put your ideas on hold. Delayed plans that need to be modified are better than unevaluated suggestions buried without a trace.
Perspective Can be a Good Thing
You’ll never understand their motives if you don’t explore your stakeholders’ views. And if you don’t understand their reasons, you’re unlikely to engender change. It is crucial to consider context, experience, politics, priorities, targets, self-interests, misunderstandings, and the color of everyone’s perspectives. Often real agendas can stay hidden.
So please get to know your stakeholders, explore their perspectives, and, most importantly, show that you care. You may not always get the whole truth or all of their thoughts, but you’ll get closer if you ask than if you don’t.
Improvement Tools Should be Use to Add Value
For Lean Six Sigma projects, as with most things in life, it’s crucial to use the appropriate tools from your toolbox rather than employing methods solely for their own sake. Through trial and error, after-training experience, and proving your command of skills for Lean Six Sigma certification, you’ll learn how to use tools as effectively as possible. You’ll be astonished at the level and rate of development you can make if you’ve chosen the correct tools. Utilize DMAIC (a Six Sigma methodology) only when necessary. Go ahead and do it if the answer is the right one.
Conclusion
It’s a question of that should we implement lean six sigma in our company or not. And if we do, how to implement it in the right way? To sort this issue out, we explained the top 10 worthwhile lean six sigma tips for having a better understanding of how to plan things while implementing this methodology in your company. Once you have a better understanding of these sigma tips you can adapt lean six sigma best practices to your business.